中国制造的不足,究竟在哪里
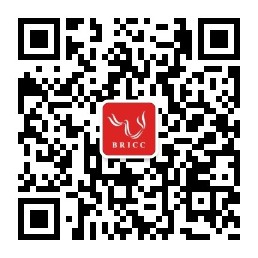
中国丝路通,是全球第一家基于微信系统的大型投融资并购项目交流平台,它提供了强大的项目发布与搜索功能、强大的会员通讯录功能,解决了留项目——项目信息驻留问题,留人——群友流动性大问题。
相信所有关心中国制造业的人都会问如题所示的问题:中国制造的不足,究竟在哪里?对于这个纠结于国人心中的问题,主流专家和媒体认为:
1.创新不足
中国制造企业创新不足,缺乏自主创新能力,长期的山寨使得中国制造业长久以来缺乏核心技术,因此必须加大科技创新的投入力度(正因没钱搞研发才山寨,专家建议没有帮助)。
2.质量低劣
中国制造企业应该增强品质意识,完善质量管理体系,并且增加设备投入以保证产品质量稳定(现在的产品性价比最高,价格上去了销量就下来了)。
3.效率低下
中国制造以劳动密集型产业为主,随着人口红利的消失,企业用工成本上升,因此必须采取机器换人战略,用机器人代替工人进行简单重复劳动(现阶段用工最多的是组装环节,但是机器人无法胜任)。
4.产业低端
中国制造业大都在产业链低端,从事低附加值生产,因此需要大力发展高新产业,进军高端市场,淘汰落后产能和落后产业(日本,法国,西班牙甚至瑞士都保留了大量传统手工业,但是附加值极高)。
上述对于中国制造业现状的评判虽并无明显漏洞,但是这些观点并不能帮助制造企业转型升级,企业需要更多可操作性强的方法论来指导其转型。
首先我们需要摘掉有色眼镜,客观地评价中国制造业的发展现状:
1.中国制造基本上处于世界前列,但各行业发展不均衡
这看似是个讨巧谄媚的说法,但是如果客观地评价中国制造发展现状,我们会发现中国制造业平均发展水平仅落后于美国,西欧和日本,基本上与东欧和韩国接近。
中国有完整的工业体系,但是发展极不平衡:国家战略相关产业领先,民生相关行业落后。例如,航天工业与西欧相当,而汽车工业发展水平甚至可能不如印度。造成这个局面的根本原因在于建国后的先军政策,此处不展开论述。
2.中国制造企业量产经验丰富,但过度依赖批量
作为世界工厂,中国制造商具备超强的大规模生产组织能力,品质管理能力和成本控制能力。中国优秀的民营制造企业可以迅速地把产品设计方案转化为生产方案,其试制,投产,量产速度世界第一。
中国制造业是伴随着全球经济上升周期和本土消费扩张而崛起的,因此在过去的30年里,对于中国制造企业而言,无论是国内还是国外,中低端产品的市场容量几乎是无限的。现在的企业家普遍坦言当时赚钱容易,只要有技术,有订单,有设备,做出产品就能卖钱。这也使得制造商长久以来形成了薄利多销的商业哲学,认为只要有规模,管理严格,把成本降至最低就可以独步天下。这个模式在过去的30年的确成就了一批优秀的制造企业,如海尔,格力,富士康等。
在这样的市场环境中厮杀出来的中国制造业具有一个鲜明的特征,那就是当经济形势好的时候可以野蛮生长,快速占领市场,并挤压竞争对手的生存空间;当经济下行,订单减少时企业就会面临极大的困境,就会因为资金链断裂而轰然倒塌。
3.工程建造经营丰富,但过度政府导向
过去40年的经济增长政府起到了很大的主导作用,除了基础设施建设外,还有许多重大攻关项目,这些基建项目和国家项目在很大程度上锻炼了一批相关的工业企业,特别是建造类企业,如高铁,发电设备,工程机械等。许多优秀的企业积累了复杂系统设计能力和复杂工程的项目管理能力,即便在世界范围,具备这种能力的企业也没有几家,而且发达国家政府也没有能力去投资和实施复杂的系统工程项目。副作用就是导致政府过度热衷于引导市场,而企业把精力过度集中在政府项目,而忽略了市场诉求。
所以,当政府呼吁企业搞智能制造,机器人,互联网+的时候,企业老总纷纷响应,甚至不惜代价。因为太多企业习惯了跟党走,听党的话,不惜赴汤蹈火,为国接盘,热衷于赚国家的钱,认为国家会买单。相比市场,更多老板更相信政策。
由于中国制造业良莠不齐,实际上现在面临最大困境的是那些从事中低端制造的企业。这些企业通常缺乏技术和产品战略,缺乏资金,在转型问题上陷入迷茫。那么这些低端制造的症结究竟在哪里?
1.质量:质量达标,品级不高
通常中国制造给人质量低劣的印象,但实际上并非如此。一般情况下,中国产品的品质是达标的,但是品级不高。中国企业可以用很低的价格制造出质量还过得去的产品,但是无法生产出性能更强,附加值更高的产品。
中国人可以用几万块钱造出质量还过得去的车,但是如果让它造一辆顶级跑车,中国企业是茫然不知所措的,连钱往哪花都不知道。
所以,企业在产品升级时应注意功能的提升,而不只是价格或性价比。
2.技术:中国企业有技术,但缺乏技术运用的想象力
很多人诟病中国企业不重视技术投入,没有核心技术,所以产品缺乏竞争力。实际上中国制造企业已经积累了不少工艺经验和技术,但是无法灵活运用现有技术创造出高价值量的产品。
实际上,绝大多数产品是不需要什么高科技的,但是需要对若干技术进行综合运用,即在技术平台上开发不同产品。通用型机电产品和民用产品都属于这个范畴,所以对于大多数中国制造企业来说,技术升级和产业转型的第一步就是梳理现有技术,并合理构建技术平台,确立技术发展路线,最后制定合理的产品战略。而不是一味地通过海外并购或技术引进获得所谓的核心技术。
3.产品:种类单一,柔性不足
中国制造企业擅长大批大量的生产模式,当达到一定产量后,生产效率,品质稳定性,生产成本控制以及生产系统各方面的协调都达到最佳状态。但是,如果批量小,企业或者做不了或者报价极高,原因是企业缺乏柔性的制造系统。
好几年前,我在天津急需20多根DIN标地脚螺栓,找遍当地五金市场就是没有,所有的厂家都说1万根起订。我当时十分诧异,那么多做螺栓的企业竟然没有一个有车床的。而在国内,很多航空和高铁上使用的非标紧固件的确价格极高,这恰恰反映出我国制造业柔性不足,无法应对市场变化的现状。
对于中小型制造企业而言,增加企业生产柔性是代价最小,风险最小,见效最快的升级策略。
4.设备:缺乏辅助工具和专用设备
中国企业买设备还仅停留在标准机采购范畴,欠缺对设备和工具的灵活运用能力,而这个缺陷实际上是由于生产工艺的欠缺所导致的。在发达国家的制造企业中,工装夹具等辅助工具大都是企业自己设计开发的,或是外包给专业的工程技术咨询和设计公司,而好的辅助设备可以极大发挥设备的性能。所有优秀的制造企业都是工具和设备设计专家。
欧洲制造企业通常会在公司内部测试一些新的生产工艺,为了实现工艺要求,企业内部钳工会自制一些辅助工具,再在通用型设备上对新工艺进行测试并改进整个生产工序。一旦工艺定型,制造企业就会要求设备供应商或自动化集成商根据自己的工艺要求和工装夹具尺寸设计专用生产设备或生产系统。
工艺改进,工装设计,设备开发是制造企业技术升级永远正确的途径。这个策略特别适合零部件供应商,因为这类企业面向专业客户,经常需要解决特殊的技术难题。产品相对简单,生产系统复杂性较低。中国大部分代工厂就是这种类型企业,非常适合走工艺设备升级路线实现转型。
总之,中国企业在转型升级时切勿盲目跟风,切勿投入到自己完全不熟悉的行业,一定要根据自身技术水平,市场定位和产品策略,整合企业资源选择合适的转型升级之路,更重要的是,在制定转型战略的时候至少要保证分析逻辑正确,数据准确,在定量化权衡利弊后再做决定。拍脑门式的指点江山,当机立断在气势上虽然很拉风,能够显示企业家的领袖风范,但是当今的制造业商业环境是个复杂的体系,缺乏量化分析的任何决策都是赌博。
(来源:工业精神)
文章很好,打赏犒劳作者一下
